AXIS -02 Telecom surveying robot
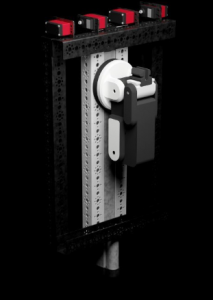
PROBLEM
Broadcasting antennae can be seen everywhere, all around the world. Providing a medium for communication services such as radio, TV broadcasting, emergency medical services, GPS and cellular phone antennas. The height of these towers can range from 30 meters to 300 meters. Considering the nature of these towers, they require regular maintenance. For such jobs, humans are put forward to climb ladders 300 meters tall to survey towers. This poses a significant risk of fatal injuries to the climbers. As a matter of fact, there have been numerous reports of deaths caused by scaling these towers, as reported by Frontline.
REPORTS
- November 22, 2013, Optical Network Technologies, Wichita, Kansas. A 25- year-old worker performing cell tower maintenance was killed when he fell 50 feet.
- 55-Year-Old Communications Tower Worker Killed After Falling 60 Feet. NIOSH, New Jersey Case Report: 08NJ052, (March 10, 2010).
- January 4, 2013, Ws Consulting & Construction, Mount Vernon, Washington. Employee fell 80 feet and died, had fall protection gear on, but the fall protection anchorage points failed.
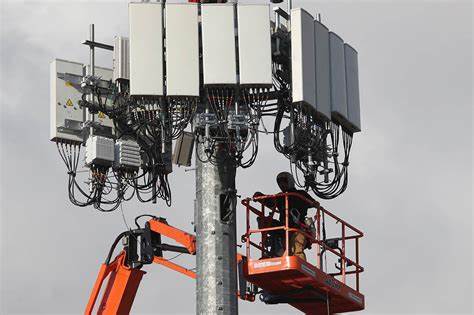
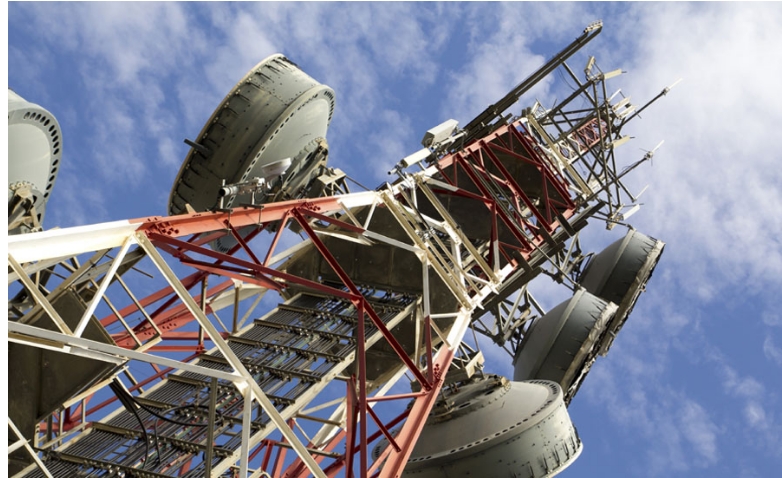
Solution
Ultimately eliminating the danger that comes with climbing a tower.
Seeing the risks posed, we conceptualized a “Telecom surveying” robot. This robot would be able to climb the entire length of a tower. With a camera and an arm mounted onto it, it can be controlled by a trained employee who can access the camera feed from the app developed specially for this robot. The arm can help analyze the tower more intimately with the help of special tool heads designed. The arm will help in the installation of various equipment onto the tower hence making it more time efficient.
The implementation of this robot can help mitigate the number of deaths. It can reduce the number of fatal injuries at a tower site to zero. The technology industry constantly evolves, dishing out new innovations at a moment’s notice. Its ever-changing landscape demands the installation of new equipment on these towers. This robot not only makes the installation safer but also faster, making logistics efforts more efficient.
INCEPTION
While researching, we came upon the many dangers that come with scaling a tower site. As young engineers, we decided to play our part to put forth a solution that would help decrease the fatalities or at the very least help diminish the dangers.
We decided to put a robot in the human’s place. It would not only decrease the dangers of working at a tower site but also prove to be a more time-efficient process. To receive professional opinion on the telecommunication towers industry, we approached.Mr. Abdul Jaleel, the manager at Benchmark Communications. He gave us an insight into the Telecom industry.
Why not just use drones?

One could suggest why not use drones. Its flying capabilities would prove to be faster than a climbing robot. However, as much as technology advances, drones will remain dangerous. The propellers needed to ascend a 300m tower would be far too big to traverse through the narrow corridors of a tower. Moreover, it would require more energy and lack payload requirements.
Since towers are used in cities, offshore sites and at army sites, the usage of drones would contradict with regulations put forward against it. Additionally, varying factors like weather, altitude, and wind speed could affect its performance making it not a reliable source of ease. It’s like asking a hammer to do the job of a scalpel.
ROBOT CONSTRUCTION
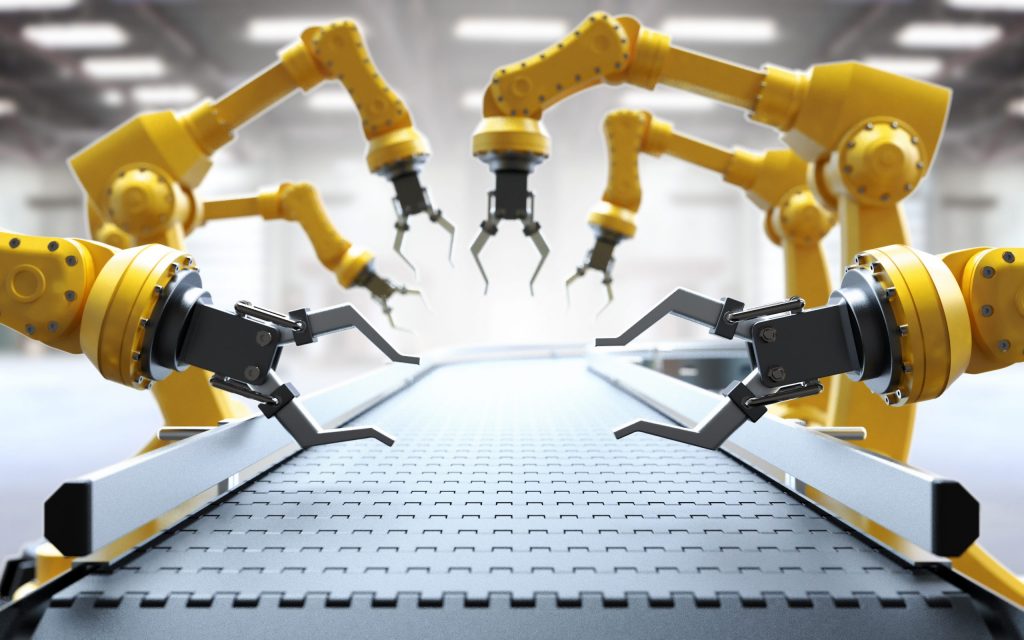
The chassis has been built using Tetrix parts which are aluminum parts cut to standard sizes. In the future, however, we aim to make an entirely custom chassis which uses parts that accordingly fit our needs. The chassis is fixed on to a linear actuator placed at, with servo motors each corner. Mounted on to the back of it, is the 3D printed arm controlled by three servo motors. All of which are controlled and programmed using the Arduino UNO R3 circuit board.
Due to the strenuous nature of climbing, we need a motor that has a lot of torque which would be needed to carry the robot vertically. Upon research, we found the linear actuator to fit most of our requirements. We chose a 45 cm linear actuator servo holding mechanism.It has the added benefit of being able to span up to 90cm once fully expanded. Our linear actuator has a torque of 1500N which can carry around 150 kg. The linear actuator is controlled by the Arduino, which according to the program will reverse the polarity with the help of two relay switches to both retract and expand.
KINEMATICS
“How does it actually work?”
To scale up the tower, the robot uses a linear actuator and two pairs of servos, which work together, enabling it to climb. It works in four stages:
- The robot with the moving servo disengages and extends, allowing it to move up.
- The robot latches on to the step of the ladder.
- The bottom servo then disengages, and the robot starts to contract.
- Once both the servos reach the top of the pole, they again latch on to it and repeats this cycle.
To scale down the ladder, the same steps are repeated in opposite order.
SDG INTEGRATION
“We have aligned our solutions with the Sustainable Development Goals to play our part in enabling a cleaner, greener future”

